Stahllexikon
Toolox 33
C | Si | Mn | P | S | Cr | Mo | V | Ni | |
---|---|---|---|---|---|---|---|---|---|
max. | 0,24 | 1,1 | 0,8 | 0,01 | 0,003 | 1,2 | 0,3 | 0,11 | 1,0 |
min. | 0,22 | 0,6 | 1,0 | 0,10 |
Toolox 33 ist ein gehärteter und angelassener Werkzeugstahl, der auf geringste Restspannungen ausgelegt
ist. Dieser Werkstoff hat deshalb eine sehr gute Formstabilität bei der Bearbeitung. Toolox 33 kombiniert
sehr gute Bearbeitungseigenschaften mit einer Härte von 300 HBW.
Der Werkzeugstahl ist speziell vorgesehen für Kunststoffformen und ist hervorragend polier- und
narbungsgeeignet.
Andere Einsatzbereiche: Gummiformen, Biegewerkzeuge, Verschleißteile und Konstruktionsteile im Maschinenbau.
Toolox 33 ersetzt die Werkstoffe 1.2311 / 1.2312 / 1.2738 / 1.7225 und ungehärteten 1.2842. | ||
---|---|---|
Härte (Garantierter Wert) |
HBW 275 - 325 (entspricht ca. 26 - 32,5 HRC) | |
Kerbschlagarbeit (Garantierter Wert) |
Prüftemperatur 20°C |
Kerbschlagarbeit Charpy-V in Querrichtung ≤ 130mm mind. 35 J |
Zugfestigkeit (Umgerechneter Wert) |
Zugfestigkeit ca. 860 - 1010 MPa | |
Ultraschallprüfung (Garantierter Wert) |
Nach EN 10 160 (Bleche) oder EN 10 228-3 (Schmiedeteile) und zusätzlichen Anforderungen gemäß SSAB V6. | |
Ätzeneigenschaften (Garantieverpflichtung) |
Toolox 33 erfüllt die Anforderungen gemäß NADCA 207–2006. | |
Abmessungen | Toolox 33 wird in Blechdicken 6 - 130mm geliefert. | |
Lieferzustand | Gehärtet und angelassen bei mind. 590°C. | |
Wärmebehandlung | Nitrieren oder Beschichten ist bei Temperaturen unter 590°C möglich. Toolox 33 ist für weitere Wärmebehandlung nicht vorgesehen. Wenn dieser Werkstoff nach der Lieferung weiterer Wärmebehandlung über 590°C unterzogen wird, sind die Eigenschaften nicht mehr garantiert. | |
Prüfung | Prüfung gemäß EN 10 025 und EN ISO 6506-1. Härtegeprüft an abgefräster Oberfläche 0,5 - 2mm unter der Blechoberfläche. | |
Toleranzen | Blech: Gemäß EN 10 029 und SSAB AccuRollTech™. Rundstahl: EN 10 060 |
|
Produkte | Präzisionsflachstahl (Standard- und Sonderabmessungen), EcoPlan, P-Platten, VarioPlan und Rohmaterialzuschnitte. Maschinenbauteile und Führungsleisten individuell nach Ihren Angaben und Zeichnungen. |
Metallurgische Information
Härteverlauf
Ermittlung der Nitriertiefe NHD nach DIN 50190-3 bei Kernhärte +50 HV
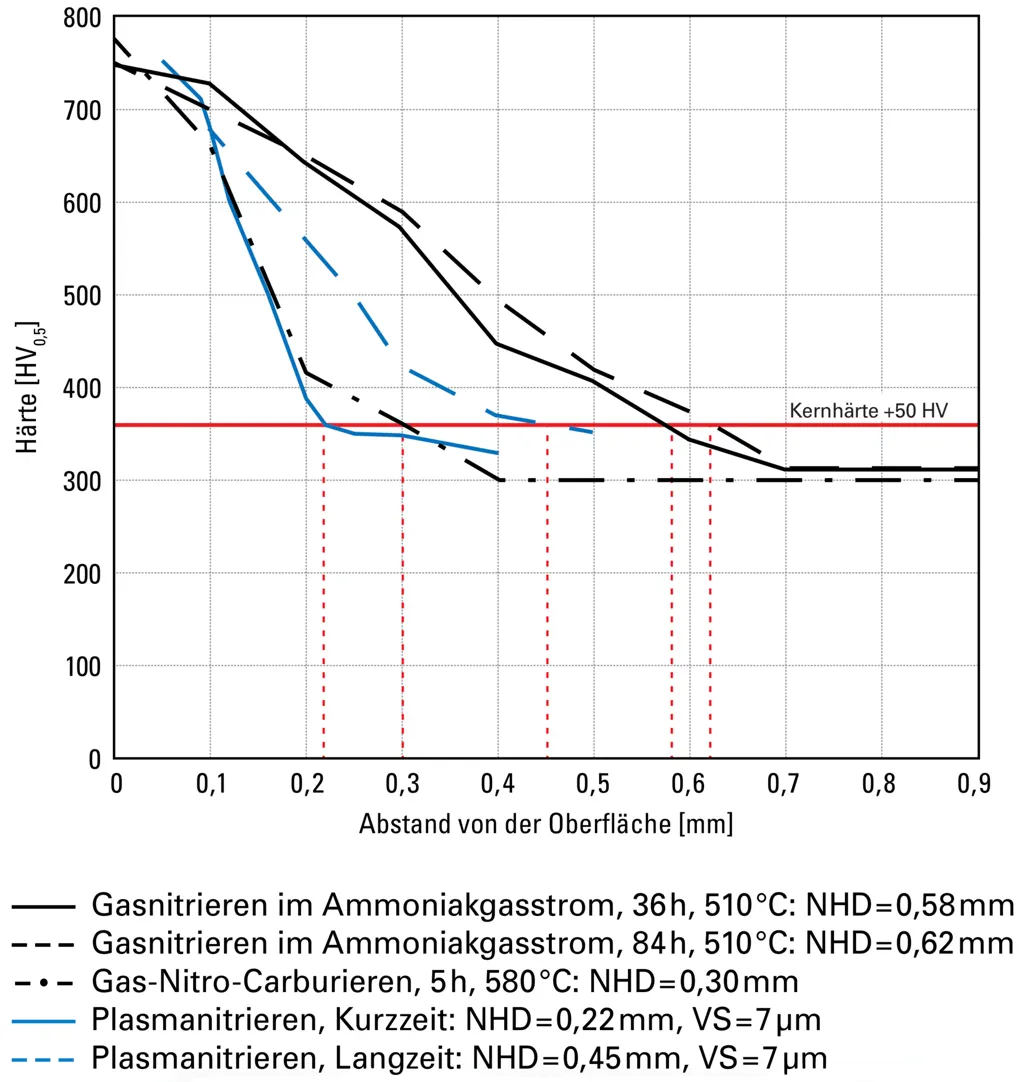
Einschlussgehalt (Typenwerte)
Einschlussquote (äquival. Durchmesser) | 6µm |
Flächenanteil | 0,015% |
Länge-Breite-Verhältnis | 1,2 |
Physikalische Eigenschaften (Typenwerte)
Wärmeausdehnungskoeffizient [10-6/K] bei +20 – 200°C: |
13,1 | ||||||
Wärmeleitkoeffizient: |
|
Kurzzeit
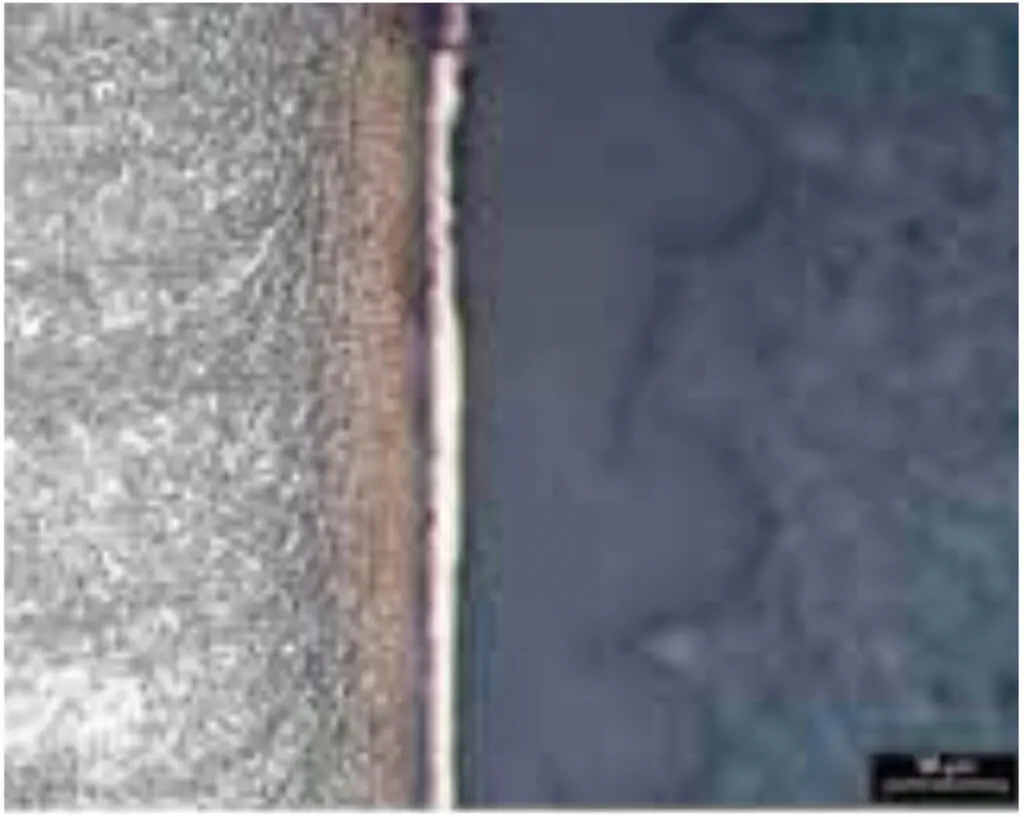
Diffusionszone,
keine Verbindungsschicht
Langzeit
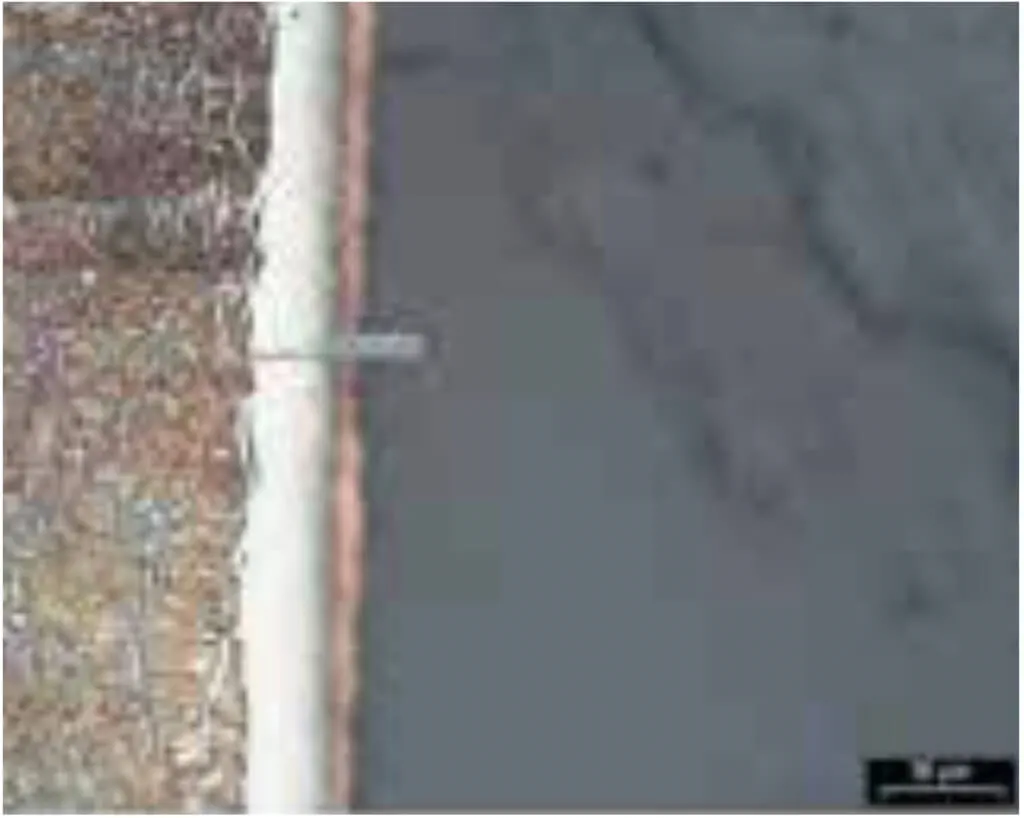
Diffusionszone,
Verbindungsschicht 36 µm
Oberflächentechnik
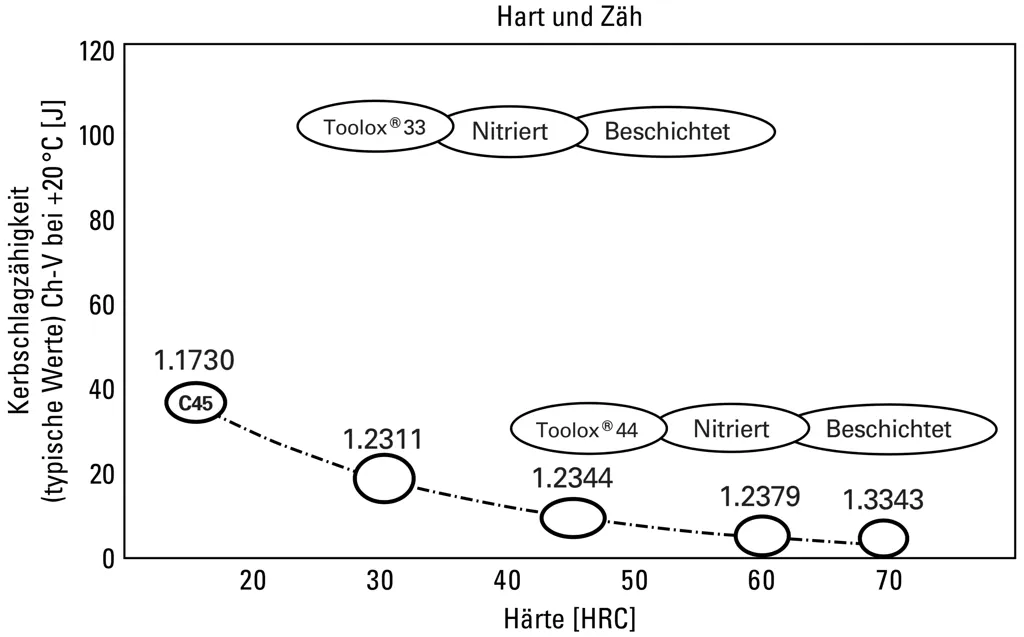
Werkzeugstandzeit beim Planfräsen
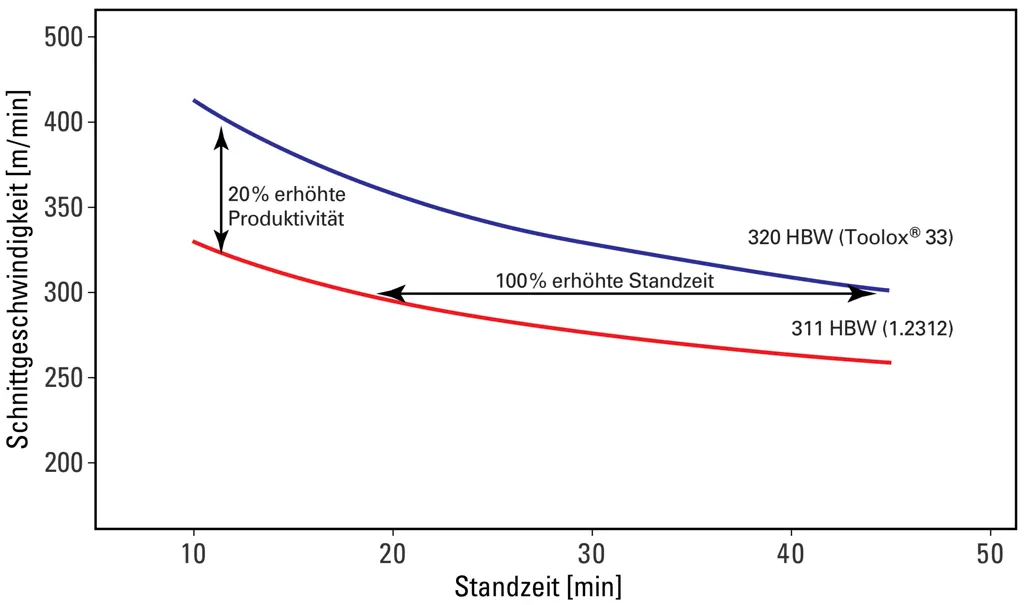
Mechanische Eigenschaften (typische Werte*)
garantierte Härte [HBW] | garantierte Kerbschlagarbeit Min [J] | Kerbschlagarbeit typ. [J]* | Dehngrenze typ. Rp0,2 [MPa]* | Zugfestigkeit typ. Rm [MPa]* | Bruchdehnung typ. As [%]* | Stauchgrenze typ. MPa* | Dicke [mm] | |
---|---|---|---|---|---|---|---|---|
-40°C | 27 | 6 - 130 | ||||||
-20°C | 45 | |||||||
+20°C | 275 - 325 | 35 | 100 | 850 | 980 | 16 | 800 | |
+200°C | 170 | 800 | 900 | 12 | 750 | |||
+300°C | 180 | 700 | ||||||
+400°C | 180 | 590 | ||||||
+500°C | 560 |
Toolox wird bei Raumtemperatur auf Härte und Kerbschlagarbeit geprüft.
Alle anderen angegeben Werte stammen aus ergänzenden Prüfungen und dienen nur zur Information, sind jedoch nicht garantiert.
* Richtwerte nur zur Information.
Ultraschallprüfung
Jedes Blech wird aufwendig geprüft, Zeugnisse 3.1 sind verfügbar, die internen Standards sind vielerorts strenger als der Industriestandard.
Oberflächenprüfung1)
Gemäß EN 10 160 |
Abstand zwischen parallelen Prüflinien [mm] | Zu beachtende minimale Fehlerfläche [mm²] | Maximal zulässige Fehlerfläche [mm²] | Maximale Anzahl lokaler Fehler [Anzahl/m²] | Entsprechende Stahl-Eisen- Lieferbedingungen |
---|---|---|---|---|---|
- | 100 | 1000 | 10000 | 1 | SEL 072 Klasse 5 |
S0 | 100 | 1000 | 5000 | 20 | - |
S1 | 100 | 100 | 1000 | 15 | SEL 072 Klasse 3 |
S2 | 50 | 50 | 100 | 10 | SEL 072 Klasse 2 |
S3 | 50 | 20 | 50 | 10 | SEL 072 Klasse 1 |
Randzonenprüfung2)
Gemäß EN 10 160 |
Randzonenbreite2) [mm] | Zu beachtende minimale Fehlerlänge [mm] | Maximal zulässige Fehlerlänge [mm] | Maximal zulässige Fehlerfläche [mm²] | Maximale Anzahl Fehler pro m Länge | Entsprechende Stahl-Eisen- Lieferbedingungen |
---|---|---|---|---|---|---|
E0 | 50 - 100 | 50 | 100 | 2000 | 6 | - |
E1 | 50 - 100 | 25 | 50 | 1000 | 5 | SEL 072 Klasse 3 |
E2 | 50 - 100 | 20 | 40 | 500 | 4 | SEL 072 Klasse 2 |
E3 | 50 - 100 | 15 | 30 | 100 | 3 | SEL 072 Klasse 1 |
E4 | 50 - 100 | 10 | 20 | 50 | 2 | - |
1) Die Prüfung kann bestellt und durchgeführt werden als Gesamtprüfung, beispielsweise E1S1 oder E2S2, oder als Nur-Randzonen oder Nur-Oberflächenprüfung, beispielsweise E1 oder S1.
2) Die Breite der Randzone bei der Randzonenprüfung variiert in Abhängigkeit von der Dicke des Blechs.
Die Dickentoleranzen der Bleche gemäß AccuRollTech™ sind enger als DIN EN 10 029.
Nenndicke [mm] | Toolox Toleranzklasse C [mm] | Maximaler Dickenunterschied im Blech [mm] | |||
---|---|---|---|---|---|
min | max | ||||
- | 4,9 | -0,0 | +0,7 | 0,5 | |
5,0 | - | 7,9 | -0,0 | +0,8 | 0,6 |
8,0 | - | 14,9 | -0,0 | +1,0 | 0,7 |
15,0 | - | 24,9 | -0,0 | +1,2 | 0,8 |
25,0 | - | 39,9 | -0,0 | +1,5 | 1,0 |
40,0 | - | 79,9 | -0,0 | +2,4 | 1,1 |
80 | - | -0,0 | +3,2 | 1,2 |
Toolox-Bleche haben eine erstaunliche Ebenheit.
5,0-7,9 | 8,0-14,9 | 15,0-24,9 | 25,0-99,9 | 100,0-155,0 | ||
---|---|---|---|---|---|---|
Toolox 33 | Quartoblech Klasse S Messlänge 1.000mm |
4mm | 3mm | 3mm | 3mm | 4mm |
Quartoblech Klasse S Messlänge 2.000mm |
8mm | 6mm | 6mm | 6mm | 8mm |
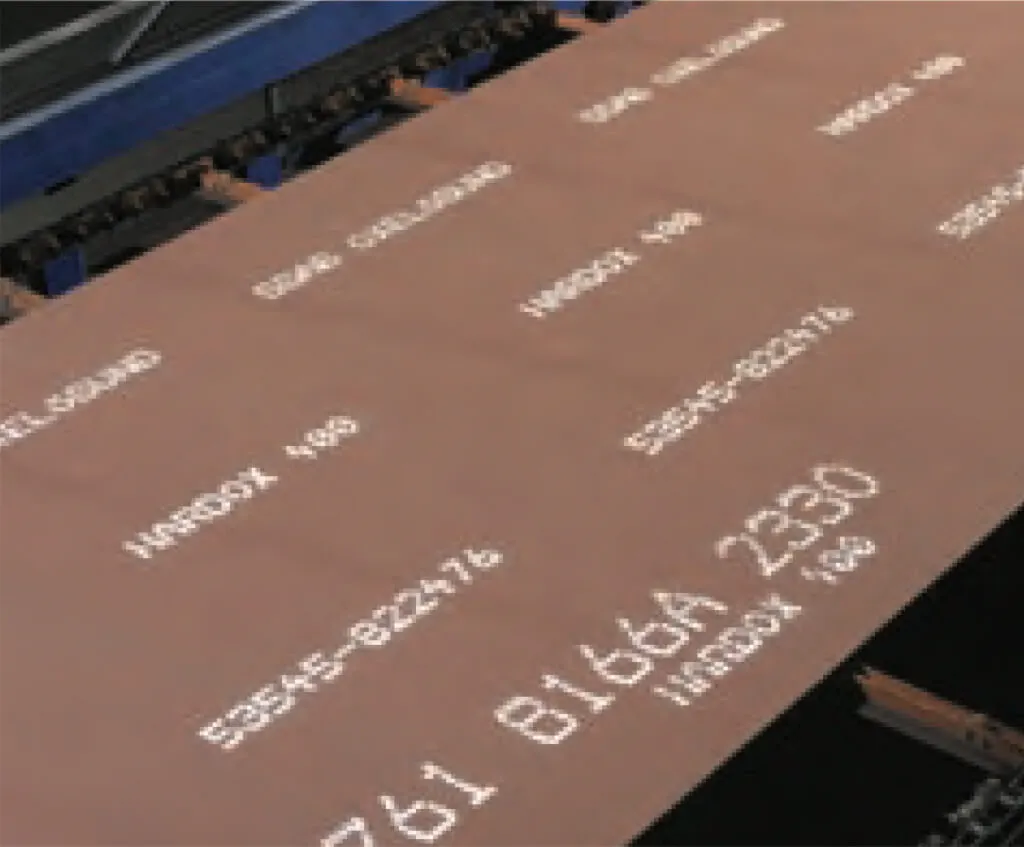
Bleche aus Toolox haben standardmäßig einen Rostschutzanstrich sowie eine Einzelblech-Kennzeichnung.
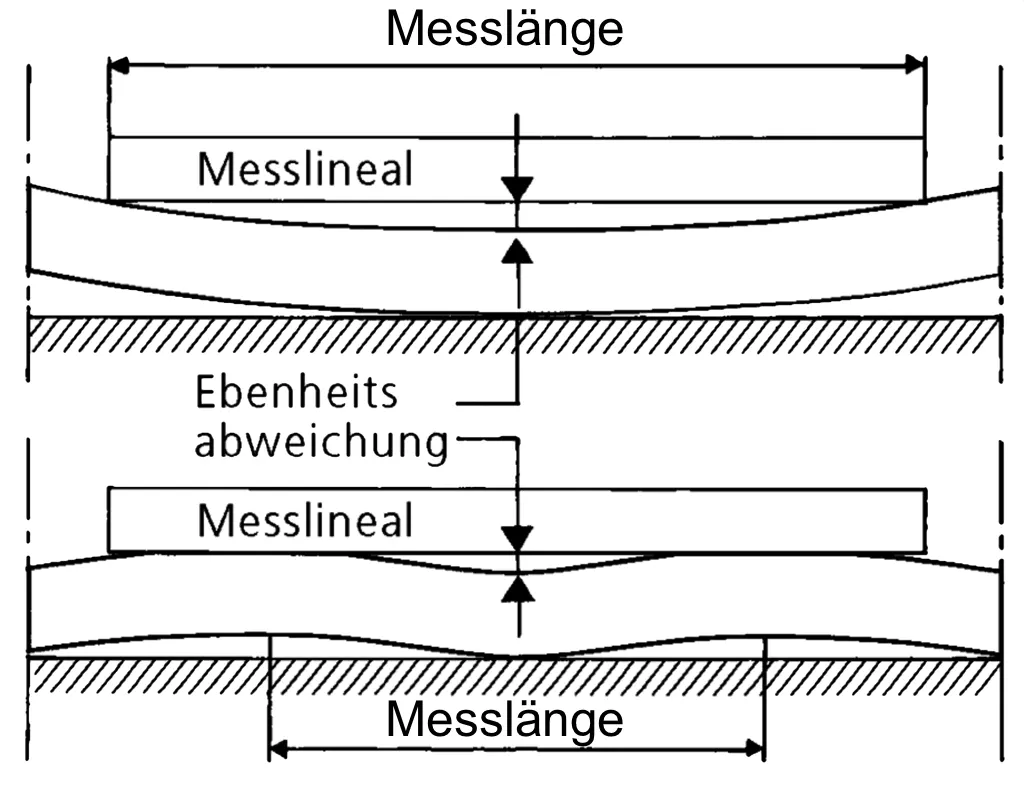
Bearbeitung von Toolox
Alle bedeutenden Werkzeughersteller sind heute auf die Bearbeitung von Toolox vorbereitet. Es empfiehlt sich, sich über geeignete Werkzeuge und Schnittwerte beraten zu lassen. Diese Empfehlungen sollten lehrbuchmäßig eingehalten werden, um ein optimales Ergebnis und produktive Leistung zu erzielen. Es ist unbedingt zu vermeiden, aus falsch verstandener Vorsicht den Vorschub zu reduzieren. Gute Spanbildung führt zum Erfolg, Toolox dankt es Ihnen mit langer Werkzeugstandzeit und schnellerer Bearbeitung.
Bohren
Das Bohren mit HSS-Werkzeugen ist weniger stabilen Maschinen sowie geringen Stückzahlen vorbehalten. Bewährt haben sich HSS-Co-Werkzeuge mit den unten angegebenen Schnittwerten. Achten Sie auf kontinuierlichen maschinellen Vorschub und scharfe Werkzeuge. Eine ausgespitzte Querschneide wäre vorteilhaft um optimale Spanbildung zu gewährleisten.
Toolox 33 | |
---|---|
Schnittgeschwindigkeit: v [m/min] | ∼ 15 |
Durchmesser [mm] | Vorschub: f [mm/U] / Drehzahl [1/min] |
5 | 0,10/950 |
10 | 0,10/475 |
15 | 0,16/325 |
20 | 0,23/235 |
25 | 0,30/195 |
30 | 0,35/165 |
*35 | 0,40/136 |
*40 | 0,45/119 |
Bohren mit VHM-Werkzeugen ist produktiv und effizient. Dabei ist eine innere Kühlmittelzufuhr mit fetterer Konzentration zu empfehlen. Achten Sie darauf, mit kontinuierlichem Vorschub zu bohren (nicht geringer als die Empfehlung des Werkzeugherstellers).
Toolox 33 | ||
---|---|---|
Schnittgeschwindigkeit: v [m/min] | 65–90 | |
Durchmesser [mm] | Vorschub [mm/U] | |
min.-max. | Startwert | |
3,0 – 5,0 | 0,08 – 0,15 | 0,10 |
5,01 – 10,0 | 0,09 – 0,16 | 0,12 |
10,01 – 15,0 | 0,16 – 0,22 | 0,18 |
15,01 – 20,0 | 0,22 – 0,28 | 0,25 |
HM-Wechselschneidköpfe oder gelötete Schneiden kommen bei mittleren Durchmessern zum Einsatz. Schnittwerte entnehmen Sie der Tabelle.
Toolox 33 | ||
---|---|---|
Schnittgeschwindigkeit: v [m/min] | 50-80 | |
Durchmesser [mm] | Vorschub [mm/U] | |
min.-max. | Startwert | |
7,5 – 12,0 | 0,10–0,16 | 0,13 |
12,01 – 20,0 | 0,15–0,23 | 0,20 |
20,01 – 25,0 | 0,18–0,27 | 0,22 |
25,01 – 30,0 | 0,20–0,30 | 0,24 |
Überlange Bohrungen bis zu über 50 x D können auch auf Bearbeitungszentren mit IKZ sehr produktiv hergestellt werden, wenn man VHM-Bohrer mit spezieller Geometrie verwendet. Typische Schnittwerte zeigt die nachstehende Tabelle.
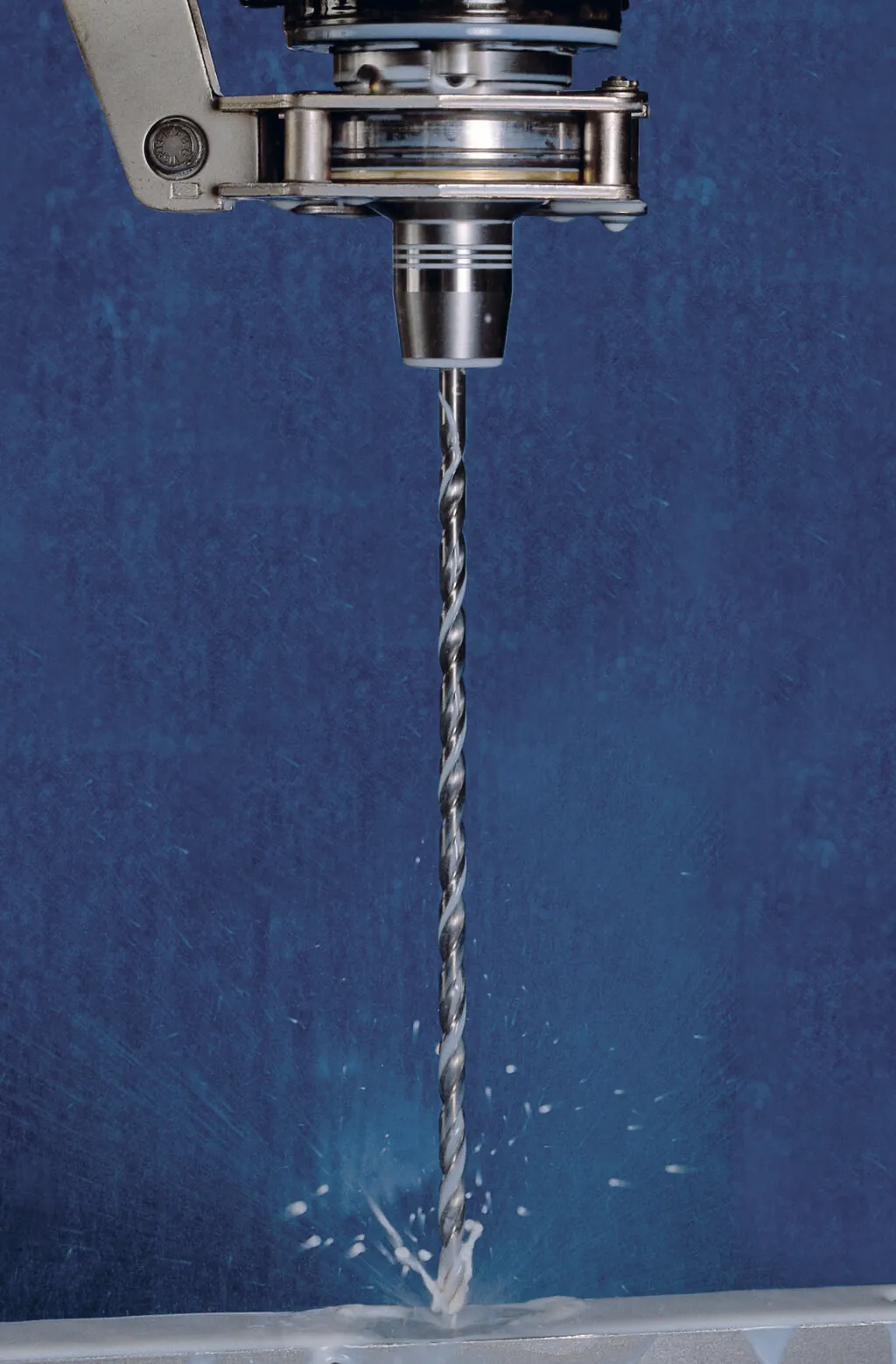
Werkstoff | Härte | Drm. | Tiefe | rel. Tiefe | Schnittdaten | Kühlung | ||
---|---|---|---|---|---|---|---|---|
d [mm] | l [mm] | l/d | vc [m/min] | f [mm] | vf [mm/min] | Emulision | ||
Toolox 33 | 300 HB | 5 | 10 | 20 | 50 | 0,15 | 477 | IK, p=20bar |
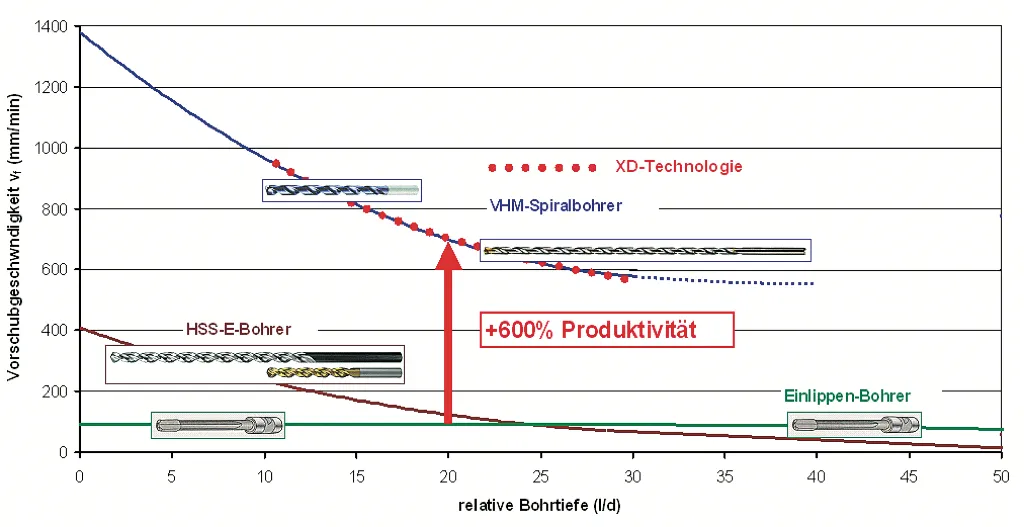
Tiefbohren in Toolox stellt eine besondere Herausforderung dar, die der renommierte Hersteller Botek mit einer besonderen Schneidengeometrie beherrschbar macht und wirtschaftlich löst. Die Einlippen-Vollbohrwerkzeuge Typ 110 mit Sondergeometrie für Durchmesser bis 12,0mm sowie Einlippen-Tiefbohrwerkzeuge Typ 01 mit wechselbaren Schneidplatten und Führungsleisten in Sonderausführung ab Durchmesser 12,0mm haben sich als hervorragende Lösung bewährt.
Für weitere Informationen kontaktieren Sie bitte Fa. Botek und beziehen sich gerne auf uns.
Bohr-∅ | 3 | 4 | 5 | 6 | 7-8 | 9-10 | 11-12 | >12 |
---|---|---|---|---|---|---|---|---|
Schnittgeschwindigkeit [m/min] | 50 | 50 | 50 | 50 | 40-50 | 40-50 | 40-50 | 40-50 |
Vorschub [mm/U] | 0,005 | 0,01 | 0,015 | 0,0175 | 0,02 | 0,03 | 0,04 | 0,1 |
Kühlschmierstoffdruck [bar] | 100 | 100 | 100 | 90 | 80 | 70 | 60 | 40 |
Anbohr-Strecke [mm] | 40 | 40 | 50 | 60 | 60 | 70 | 70 | 70 |
Anbohr-Vorschub [mm/U] | 0,0025 | 0,005 | 0,0075 | 0,009 | 0,01 | 0,015 | 0,02 | 0,05 |
Erreichbarer Standweg mit Öl: ca. 10 – 12 Meter bei optimalen Prozessbedingungen
Fräsen
Toolox ist aufgrund äußerst geringer Eigenspannungen besonders verzugsarm, wenn man mit optimalen Parametern zerspant und keine unnötige Wärme ins Werkstück bringt. Lange Standzeiten erreicht man durch geschickte Frässtrategie und stabile Aufspannung sowie stets hinreichende Spandicke. Toolox hat eine besondere Gefügestruktur, die die Bearbeitung trotz der hohen Härte erleichtert. Karbide sind sehr harte und verschleißbeständige Gefügebestandteile. Deren mikroskopisch feine, kugelige Form im Toolox-Gefüge vermeidet die bei anderen Werkzeugstählen typische Schneidenschädigung. Ein hinreichend hoher Zahnvorschub sichert das Abtragen der Karbide gemeinsam mit dem Span, ein zu geringer Vorschub würde dagegen zu intensivem Abrasivverschleiß an der Schneide führen. Scharfe Schneiden mit positiver Geometrie sind optimal für Toolox. Wählen Sie Werkzeuge für die Bearbeitung hochvergüteter Stähle. Werkzeuge für die Hartbearbeitung (bis 60 HRC) sind ungeeignet, deren Schneiden haben meist negative Spanwinkel.
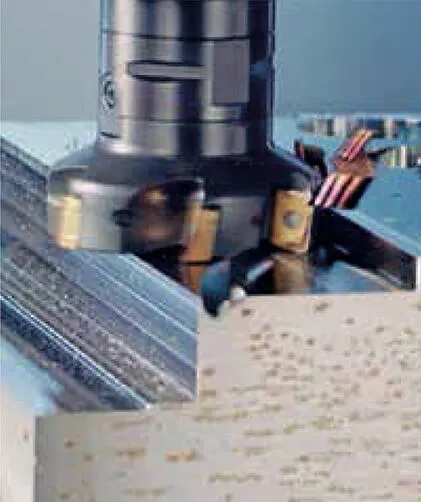
Einfahrt per "Roll-In" Verfahren
Verschleiß nach 800 Bearbeitungsgängen
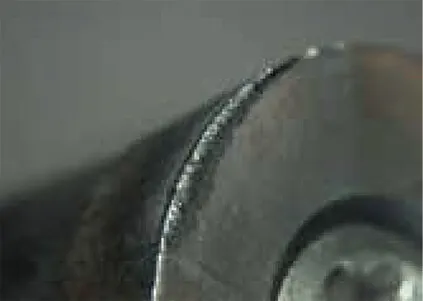
Gerade Einfahrt ins Werkstück
Verschleiß nach 390 Bearbeitungsgängen
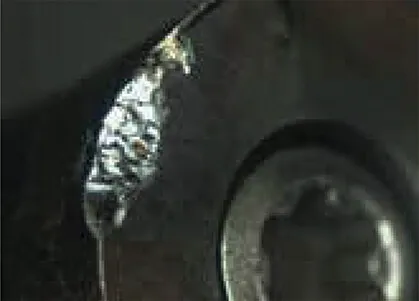
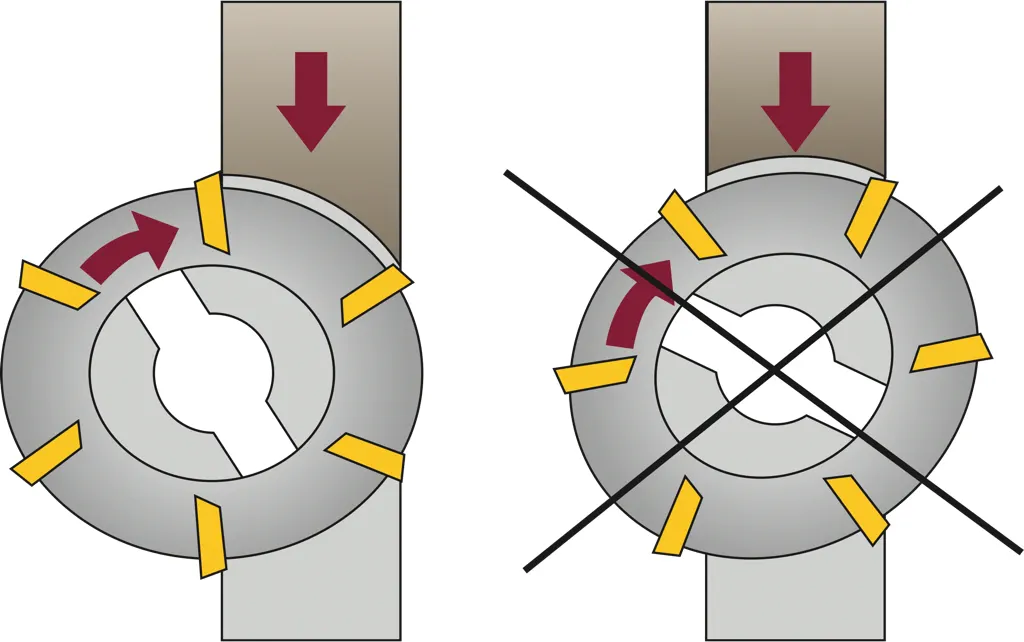
Einführen in das Schneideverfahren per "Roll-In" Verfahren
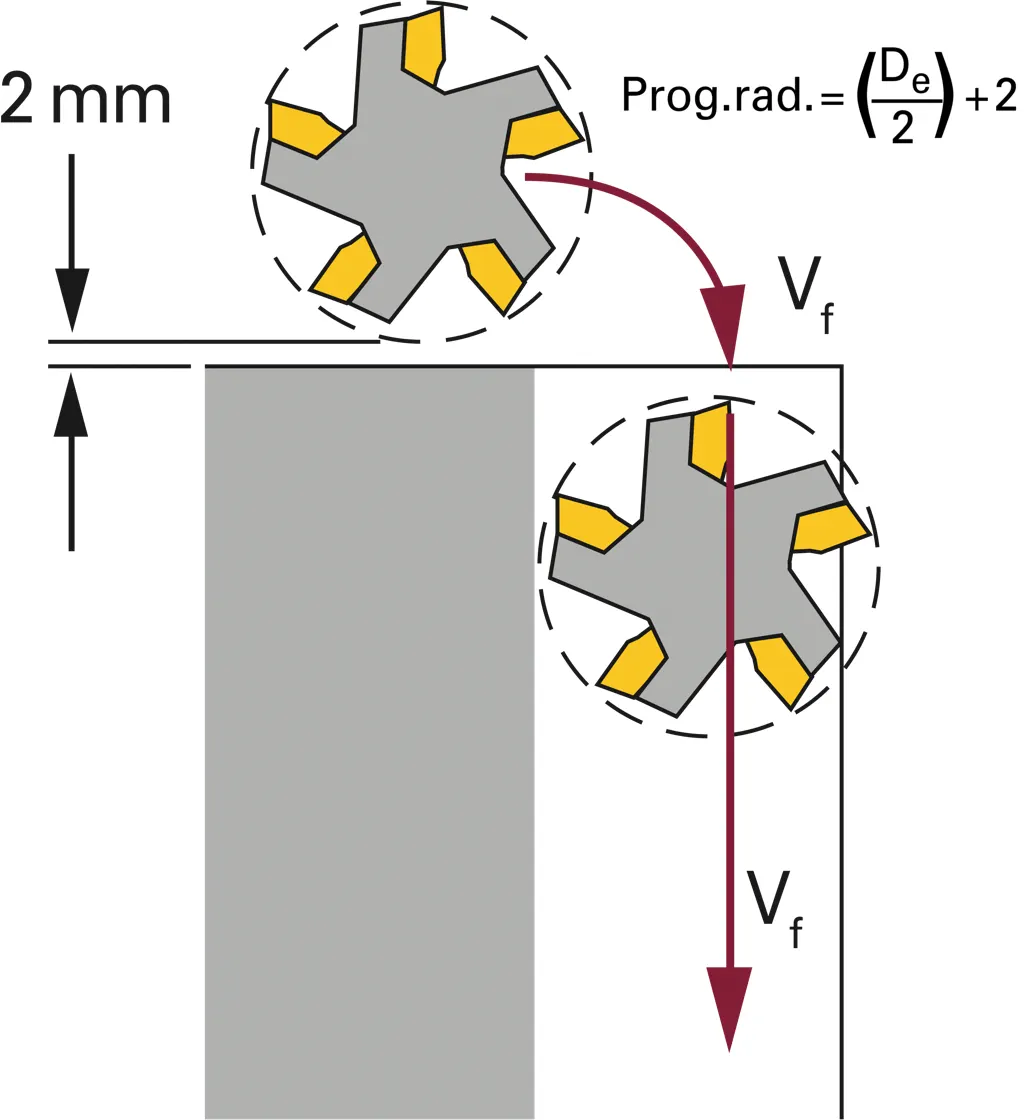
Planfräsen
Unterbrochene Schnitte fräsen sich besser mit runden Wendeplatten. Besonders hohe Produktivität erreicht man mit HPC-Werkzeugen. Auch Eckmesserköpfe sind für Toolox geeignet.
Empfehlung für 45°-Fräser
Toolox 33 | ||
---|---|---|
Schnittgeschwindigkeit: v [m/min] | 180-220 | |
Vorschub: fz [mm/Zahn] | min. – max. | Startwert |
Wendeplattegüte P30 | 0,15–0,35 | 0,25 |
Empfehlung für Planfräser mit runden Platten
Toolox 33 | ||
---|---|---|
Schnittgeschwindigkeit: v [m/min] | 180-220 | |
Vorschub: fz [mm/Zahn] | min. – max. | Startwert |
Wendeplattegüte P30 | 0,10–0,25 | 0,15 |
Empfehlung für Eckfräser / Eckmesserköpfe
Toolox 33 | ||
---|---|---|
Schnittgeschwindigkeit: v [m/min] | 180-220 | |
Vorschub: fz [mm/Zahn] | min. – max. | Startwert |
Wendeplattegüte P30 | 0,12–0,25 | 0,17 |
Schnittwerte für HPC-Kopier- und Planfräser
Werk- stoff- gruppe | Werkstoff- bezeichnung | Festigkeit N/mm2 | Kopierfräsen | Tauch- / Bohrzirkularfräsen | ||||||||||||||
---|---|---|---|---|---|---|---|---|---|---|---|---|---|---|---|---|---|---|
Trockenbearbeitung | Nassbearbeitung | Trockenbearbeitung | Nassbearbeitung | |||||||||||||||
Schneid- stoff 1. Wahl | Vc [m/min] | Schneid- stoff 1. Wahl | Vc [m/min] | Schneid- stoff 1. Wahl | Vc [m/min] | Schneid- stoff 1. Wahl | Vc [m/min] | |||||||||||
min | Start | max | min | Start | max | min | Start | max | min | Start | max | |||||||
8.2 | Toolox 33 Werkzeugstähle |
900–1100 | F25M | 120 | 140 | 160 | F25M | 110 | 130 | 150 | F25M | 80 | 90 | 100 | F25M | 70 | 85 | 100 |
Schaftfräsen
Beim Schlitzfräsen hat sich eine Tiefenzustellung ap von 0,5 x D bewährt, hinreichender Spanraum sollte vorhanden sein. Schaftfräsen bis hin zum Trochoidalfräsen ist mit ap in voller Schneidenlänge und ae von ca. 0,1 x D sehr produktiv. Trockenfräsen mit Druckluftkühlung zur Abfuhr von Spänen vermeidet Thermoschock und Überlast infolge eingezogener Späne.
Gewinde
Beide Toolox-Werkstoffe können mit Maschinengewindebohrern bearbeitet werden. Erfahrene Schlosser bohren das Kernloch etwas größer. Besonders bewährt haben sich Schneidpaste, Schneidöl oder eine fettere Emulsion.
Toolox 33 | |
---|---|
Schnittgeschwindigkeit: v [m/min] |
7-10 |
Größe | Drehzahl [1/min] |
M5 | 445–635 |
M6 | 370–530 |
M8 | 270–400 |
M10 | 220–320 |
M12 | 185–265 |
M16 | 140–200 |
M20 | 110–160 |
Gewindefräsen ist ein produktives Verfahren für hohe Fertigungssicherheit, auch bei sehr kleinen Durchmessern und gerade dort, wo Gewindeschneiden schwierig ist.
Toolox 33 | |
---|---|
Schnittgeschwindigkeit: v [m/min] |
80-110 |
Vorschub: fz [mm/Zahn] | 0,03 – 0,06 |
Flachsenken sowie Kegelsenken sind mit Wendeplattenwerkzeugen problemlos auf Bearbeitungszentren möglich. Für weniger stabile Maschinen haben sich Senker mit mitlaufenden Führungszapfen bewährt.
Toolox 33 | |
---|---|
Schnittgeschwindigkeit: v [m/min] |
0,10-0,20 |
Durchmesser [mm] | Drehzahl [1/min] |
19 | 670–1340 |
24 | 530–1060 |
34 | 375–750 |
42 | 300–600 |
57 | 225–440 |
Polieren von Toolox
- Feinschliff mit einem groben Schleifmittel (z.B. Korngröße 120). Alle Spuren der Verarbeitung oder des Erodierens werden hierbei komplett abgeschliffen. Vorzugsweise sollte hierbei die flache Seite des Schleifmittels zum Einsatz kommen. Variieren Sie die Schleifrichtung in X-Form, um eine absolut flache Oberfläche zu erzielen, Ihre Arbeit effizienter zu gestalten und gleichzeitig Zeit zu sparen.
- Feinschliff wie in Schritt 1, jedoch mit einer feineren Korngröße wie z.B. 320. Alle nach dem vorherigen Schliff noch verbliebenen Spuren werden hierbei komplett beseitigt.
- Grobpolierung mit Diamantpaste auf einem Stück Messing. Korngröße 45μm. Diese Grobpolierung wird durchgeführt bis alle verbliebenen Spuren und Kratzer des vorangegangenen Arbeitsschritts (Schritt 2) gänzlich beseitigt sind.
- Vorgehensweise wie in Schritt3, jedoch mit 15μm Diamantpaste bis alle nach Schritt 3 noch vorhandenen Spuren verschwunden sind.
- In diesem Schritt gehen Sie vor wie in Schritt 4, verwenden jetzt aber eine Diamantpaste mit 7μm. Auch dieser Schritt wird fortgesetzt, bis alle aus Schritt 4 verbliebenen Spuren entfernt sind.
- Polieren Sie mit Diamantpaste (7μm) auf einem Faser- oder Plastikelement. Fahren Sie fort bis die letzten aus Schritt 5 noch verbliebenen Unebenheiten beseitigt sind.
- Gehen Sie jetzt vor wie in Schritt 6, verwenden Sie jedoch anstelle von 7μm-Paste eine Diamantpaste mit lediglich 3μm. Fahren Sie fort bis die letzten aus Schritt 6 verbliebenen Nuancen von Unebenheiten beseitigt sind. (Wir wählen hier das Wort "Nuance", da bis jetzt die Oberfläche bereits so eben und fein ist, dass man eigentlich von keinerlei für das bloße Auge noch erkennbare Kratzer sprechen kann.)
- Polierung mit 3μm Diamantpaste auf einem Stück Filz bis alle aus dem vorangegangenen Schritt noch vorhandenen Nuancen entfernt sind.
- Als abschließenden Schritt polieren Sie jetzt mit Diamantpaste der Korngröße 3μm und Watte. Dieses ist Handarbeit und hierbei wird der endgültige Glanz erzielt. Fahren Sie fort bis die gesamte Oberfläche einen einheitlichen Glanz aufweist.
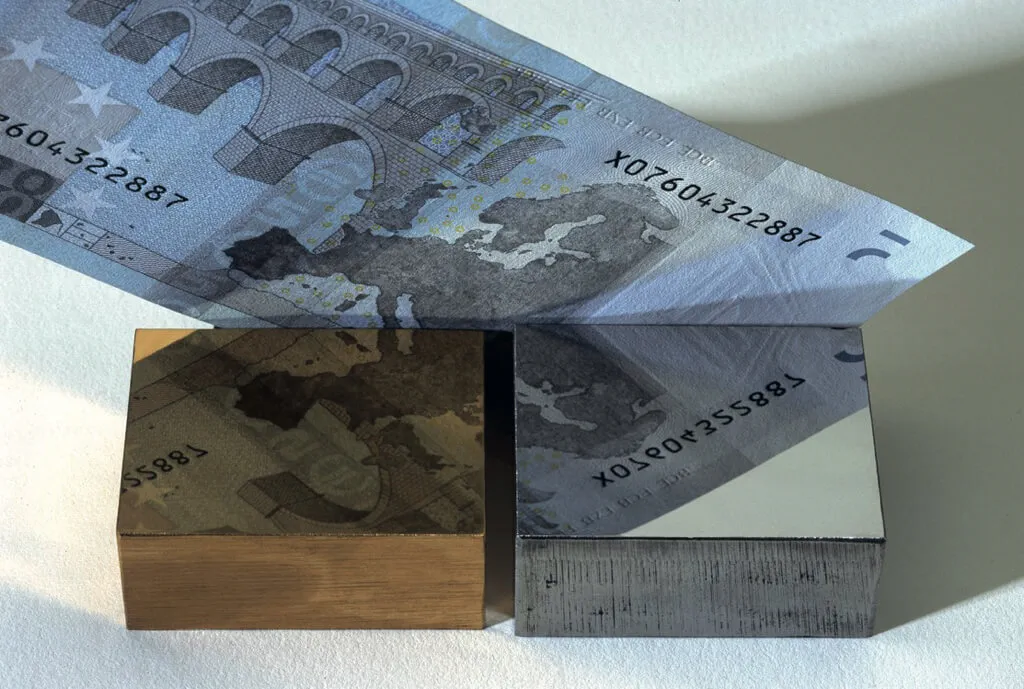
Schweißen von Toolox
Toolox ist unter Beachtung der nachstehenden Hinweise gut schweißbar. Das Kohlenstoffäquivalent ist für
Toolox 33 CEIIW 0,62–0,71 / CET 0,4–0,44.
Geeignet für das Schweißen ohne Vorwärmung sind austenitische Schweißzusätze AWS 307 oder AWS 309.
Es ergibt sich eine Festigkeit von ca. Rp0,2 = 500 MPa in der Naht.
Unlegierte oder niedrig legierte Schweißzusätze ergeben Festigkeiten bis ca. Rp0,2 = 930 MPa
und gute Zähigkeit.
-
Wärmen Sie beide Seiten der Schweißfuge vor, und zwar etwa 100 – 150mm auf jeder Seite. Die
Vorwärmtemperatur sollte in der Mitte des Bleches erreicht werden. Behalten Sie die Vorwärmtemperatur
während des gesamten Schweißvorgangs bei, insbesondere beim Heftschweißen.
- Verwenden Sie möglichst weiche oder rostfreie Elektroden. Die Elektroden müssen trocken sein. Der maximal zulässige Wassestoffgehalt beträgt 5ml/100g Schweißgut. Um eine optimale Texturbildungsqualität zu erzielen, sollte das Schweißen unter Anwendung des WIG-Verfahrens mit einem Zusatzdraht mit derselben chemischen Zusammensetzung wie der Grundwerkstoff durchgeführt werden. Die einfachste Methode besteht dann darin, eine Stange von einem übrig gebliebenen Teil des Grundwerkstoffs abzusägen.
- Schweißen Sie mit einer Wärmezufuhr, die einen Δt8/5Wert zwischen 10 und 20s ergibt.
- Beim Schweißen sollte eine Zwischenlagentemperatur von höchstens * 170°C für Toolox 33 erreicht sein, bevor die nächste Lage geschweißt wird.
- Führen Sie eine Wärmebehandlung nach dem Schweißen im Bereich von etwa 100 – 150 mm ab jeder Seite der Schweißnaht durch. Die Durchwärmzeit sollte 5 min / mm Blechdicke oder mindestens 60 Minuten betragen. Normalerweise ist eine Durchwärmzeit von 2 Stunden ausreichend. Der Beginn der Durchwärmzeit ist der Zeitpunkt, zu dem die Temperatur im gesamten Anlassvolumen erreicht ist.
* Die Wärmebehandlung nach dem Schweißen sollte mit einer Temperatur von 150 – 200 °C durchgeführt werden, falls nur geringe Anforderungen hinsichtlich der Formstabilität gestellt werden.
* Die Wärmebehandlung nach dem Schweißen sollte mit einer Temperatur von 560 – 580°C durchgeführt werden, falls hohe Anforderungen hinsichtlich der Formstabilität gestellt werden und der Einfluss der Schweißnaht auf das Texturbildungsergebnis minimiert werden soll.
Härtevergleichstabelle für Toolox und Hardox
Zugfestigkeit MPa |
715 | 790 | 820 | 861 | 935 | 995 | 1011 | 1090 | 1169 | 1245 | 1328 | 1412 | 1494 | 1580 | 1758 | 1940 | 2130 |
Vickershärte HV |
205 | 233 | 243 | 261 | 289 | 311 | 317 | 345 | 373 | 401 | 429 | 458 | 485 | 514 | 569 | 627 | 682 |
Brinellhärte HBW |
225 | 250 | 260 | 275 | 300 | 320 | 325 | 350 | 375 | 400 | 425 | 450 | 475 | 500 | 550 | 600 | 650 |
Rockwell HRC |
19 | 22,5 | 24 | 26 | 29 | 32 | 32,5 | 35,5 | 38 | 40 | 42,5 | 44,5 | 46,5 | 49 | 52,5 | 55 | 57,5 |